私たちは加工製品の品質を保証するために、
徹底的な検査フローを実施しています
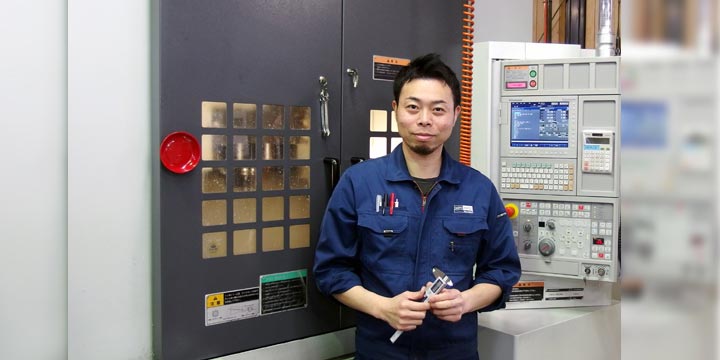
当社では “精密部品加工・小ロット生産・試作部品加工” 、これら全ての部品加工において、製作担当者による検査の後も、専任検査担当者による正確な検査を実施しています。そしてお客さまへは品質保証としてダブルチェック体制で、※高品質な製品を提供することをお約束しています。
実際の検査方法は、図面へ実測値や実施判定を記入し、検査漏れや公差外寸法がないことを確認。とくに重要箇所(幾何公差)の検査と外観検査については、全数実施しています。この他の箇所も、重要度合いに応じて検査頻度を増やしています。
※斉藤プレス「高品質な製品」の定義
- 図面に示された寸法や許容差を厳密に守ること
- 表面の仕上げや見た目が良好で、傷や汚れ、欠陥がないこと
- 製品が厳密に検査され、全数チェックや適切な抜き取り検査を行っていること
品質保証のための検査
ダブルチェック(2名体制)
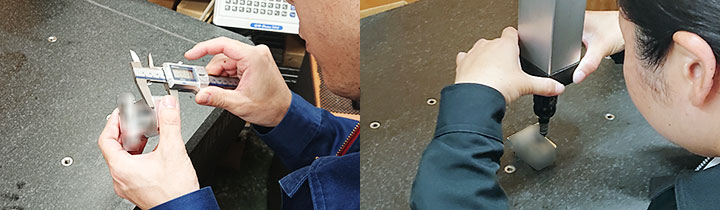
当社のダブルチェックは「加工担当者による検査」と「検査員による検査」、この2名体制で品質検査を実施しています。
まず加工担当者は、図面通りに製品が仕上がっているかを、図面の指示寸法の隣に実測値を記入し、照合しながら確認を行います。直接図面に記入することで検査漏れや公差外寸法等の不具合を発見しやすくしています。
重要ポイント!
この段階でも十分な検査が実施されていますが、さらに万全を期すために、同様の検査を改めて検査員が行います。これにより製品寸法の再確認ができるだけでなく、図面の見誤りや思い込みによる誤認識といった人為的なミスも発見することができます。
全数検査:幾何公差への対応
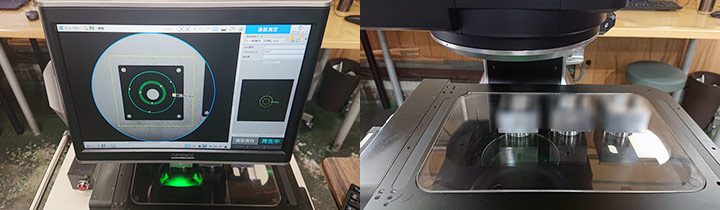
「幾何公差(きかこうさ)」とは、大きさや距離を測定する通常の寸法測定とは違い、その部品の形状や指定箇所の位置関係などを規制する公差のことです。当社で製作している量産部品の多くは、位置度・平行度・同軸度などの「幾何公差」が図面に指示されています。
重要ポイント!
この幾何公差の値は、たとえば産業用ロボット等の構成部品では、その製品の能力を確実に発揮させるための重要な要素で、厳しい公差が求められます。その分、製作をする上では管理が難しい箇所があり、精度の高いマシニングセンタで加工をしても加工機任せでは品質保証できない場合があります。当社ではそのような箇所も全数検査を実施して、品質を保証しています。
抜き取り検査:精級寸法箇所の品質管理
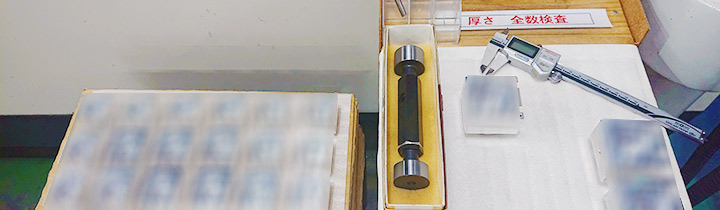
当社では、加工現場でも品質保証のための検査ルールを設け運用しています。
加工機と加工完了品置場の間に「検査待ち置場」が設置してあり、加工が終わって機械から取り出された製品は、まず検査待ち置場に加工順通りに並べられます。加工が終わってもすぐに加工完了品置場には行かず、検査待ち置場で決められた検査項目を終えてはじめて加工完了としています。合格した製品のみを次の工程に進めることで、品質の一貫性と信頼性を確保しています。
重要ポイント!
この他にも、1日三回(朝・昼・夕方)の定期検査にて、測定機を使って精級寸法箇所の検査をしています。測定箇所や注意点を詳細に記載した作業標準書を作成し、従業員が一貫して正確に測定できるようにしています。
外観検査(工程2回)
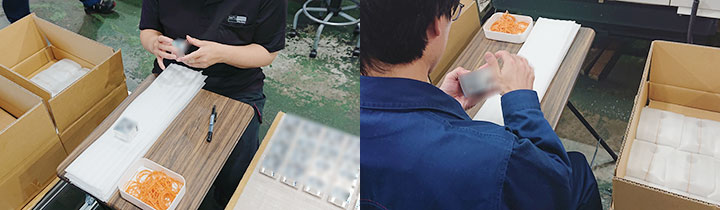
通常のアルミ部品には、加工後に表面処理(アルマイト)が施されますが、当社ではこのアルマイト工程の前と後で、2回の外観検査を行っています。
外観検査とは加工中に付いた傷や打痕、作業員の取り扱いによって付いた傷などがないか、見た目の綺麗さを確認する検査です。アルマイト工程前の検査は、修復可能な打痕などの問題を事前に修正するために行われます。アルマイト工程後の外観検査では、アルマイト工程で付いた傷やシミなどがないかを検査しています。
重点!
これら2回の検査をクリアした製品だけが出荷されるので、外観品質にも自信を持っています。
品質方針